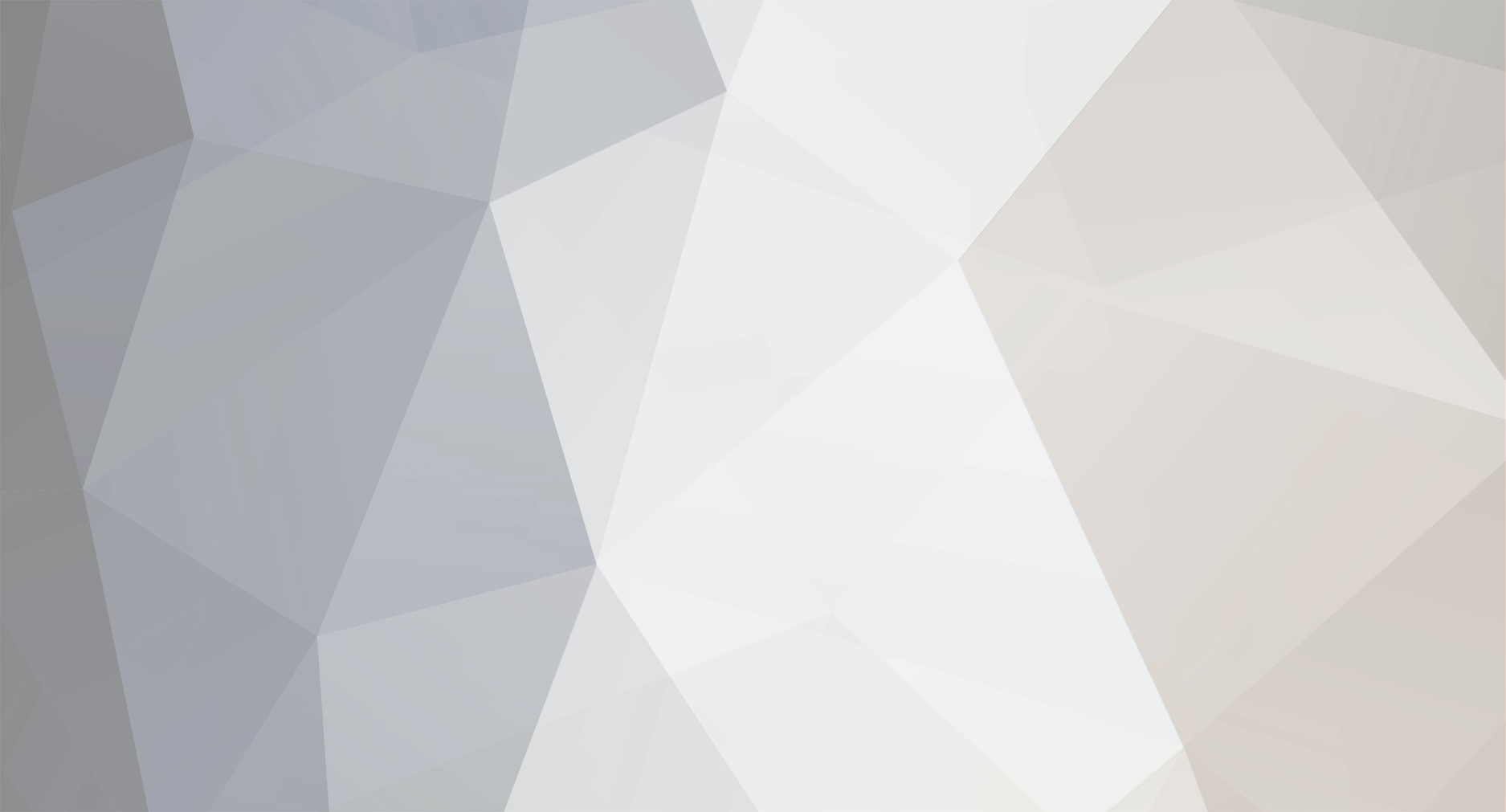
slanty
-
Content Count
68 -
Joined
-
Last visited
-
Days Won
1
Content Type
Profiles
Media Demo
Forums
Gallery
Calendar
Store
Posts posted by slanty
-
-
Thanks guys. This is all really useful perspective. It'd be awesome to know what many of these listings are actually going for - seems like the market is still adjusting downwards from what I can see - lots of good boats for sale sitting around for a looooong time.
-
Howdy all,
I'm in the hunt for an upgrade to my raven 26 (in time) to a more family friendly keeler, and am one of those blokes that can't quite make up my mind on what I'm after. I keep oscillating between gulf type cruisers to bomb proof coastal and offshore capable boats.
Lets not go there just now, but one of the boats that keep coming up are Davidson 31's. They look to have a nice layout, and seem like good value as a gulf / sounds type boat. I can't seem to find many thoughts on the either here or on the web. Anyone got any wisdom they could share?
-
I solved the two battery issue by using a sun saver duo.
https://www.morningstarcorp.com/products/sunsaver-duo/
Independent charging channels and weighting (will put 10% effort into starter and 90 into house or 50/50.)
Got mine for around $200.
-
Yea - the gold standard is actually a hall effect sensor - no physical contact like a pot so much longer life and generally better specd. Was surprised that even modern rudder position sensors are still resistors.
Thinking of springing for one of these if the pot gives me trouble:
-
Yep they are parts for making a 3d printer that are available direct. Again, the innovation of DIY manufacture of the printer themselves has spawned an industry of people supplying parts for them at very low cost.
-
Good you fullas aren't disrespectin me.
Anyway, the important components in this build arent chinese knockoffs. They are brand components with the r&d done. Pololu still manage to build a tilt roll and pitch compensated compass for 20 bucks. This is generally used in drones and other rc stuff. I think the marine engineers are getting outflanked a bit on the innovation/pricepoint factor in recent times.
Instead of moaning about that i chose to exploit it. Sorry for the typos. On a phone.
-
Sounds like a plan Winter - you'd just want to be satisfied that the B&G motor control is going to be compatible with your autopilot. IT might be in a better position to comment on that one.
-
Farrari- the ubec looks like the business. I was just going to get a dc-dc converter but I didn't think about the noise issue. Looks like this may solve it.
Didn't think about youshop - bugger! next time.
Most of my parts are chinese cheapies. All have worked great so far and quality has been fantastic for the price. I've bought the key items from US suppliers (motor controller, compass module) as there was no good generic available that I could find. Almost everything else is from banggood.com. Free shipping on everything!
warning tho - bangood is highly addictive.
-
too tall - yep the rudder sensor was my big innovation I'm quite proud of. It resides in the tillerpilot itself and is just a 10 turn poteniometer driven by the ram via 3d printer belts and pullys. That gives me 0-5v depending of the relative position of the ram (and therefore the position of the rudder). Then it's just a case of measuring the signal back at hard port, hard stbd and neutral, entering these into the code and voila - rudder position.
Obviously, this means the pilot is only able to be used on my boat and requires re calibration if used elsewhere - but not planning on that.
-
Thanks for the feedback all.
exTL - not sure my fabrication skills are quite up to doing this for money but that's very flattering. I should think the video of my compass unit in an icecream container should have erased that thought from yr mind.I'd love some other people to have a whirl at it though. it doesn't take a great deal of skill.
IT - the compass is capable of quite high speeds I think, but it's the rest of the script that slows things down. I've currently got extra print commands active in there for trouble shooting, and they slow things down a lot. Once i get rid of those, I think I'll be able to get around 10hz.
no plans at the moment for wind or GPS integration, although the original coder has done this. For the times that I would use it, dealing with all that it entails isn't really worth it for me. My first experiences on boats were with old compass autohelms and that's all i really require.
Also, i studied human factors in jet airliners as part of my psychology many moons ago - the takeaway lesson is that the more automated the system, the less situational awareness the pilot has, and the bigger screw ups as a result. Something that I can just set to set to a bearing while I look after everything else and tweak as needed is just right for keeping me engaged in what the boat is doing.
-
That's good to know. The guy who used the mechanical gimbal has achieved a within 2 degrees of error apparently in rough seas off Tassie, Would be stoked if I could get my error down to that. One advantage of a slow old boat is the error don't matter so much!
-
Only been in pretty flat seas so far, but yep, can adjust gain, deadband, motor speed (it's graduated, not all or nothing) and maximum rudder angles all through the software. So in short it takes some tinkering, but customising it to any particular boat it definately doable.
The motion of the vessel is a slightly different challenge. The IMU (compass) does compensate for pitch and heel etc, but I've seen one on a mechanical gimbal which improved its performance a lot. That's next step....
-
Not much - bit over a hundy I reckon. $30 for a motor controller, $20 for a compass module and arduino for around $30....plus some hideous shipping from the states.
-
Hi folks,
Been lurking here a while and thought i'd post on something I've been working away on for a while.
I sail a raven 26 out of the Mahurangi. I got her for a pretty sharp price and with it came a semi-defunct simrad tp10. I tried and failed to get the thing going but the electronics were toast.
I had been mucking around with arduino for a while and thought that it would make a great platform for a DIY tillerpilot using the linear actuator from the simrad (which was fine).
Someone had already done the thinking on this - all I had to do was adapt it for my circumstances.
Here's a vid I made of where I'm up to....
https://www.youtube.com/watch?v=TRd4Qv0znGw&t=109s
would love to get your thoughts....
Jim
Navman chartplotter screen v v dark
in TechTalk
Posted
I had this happen. it is the backlight. Difficult to know whether its the little flourescent tube or the driver that has failed, and you don't know until you replace both unless you can test with an oscilloscope, and even then it's not super easy to diagnose.
I replaced mine with an led backlight but you lose control of the brightness via the software and the repair in my case at least looks very home brew - I've probably lost waterproofness in the unit for one but it suits me for the moment.