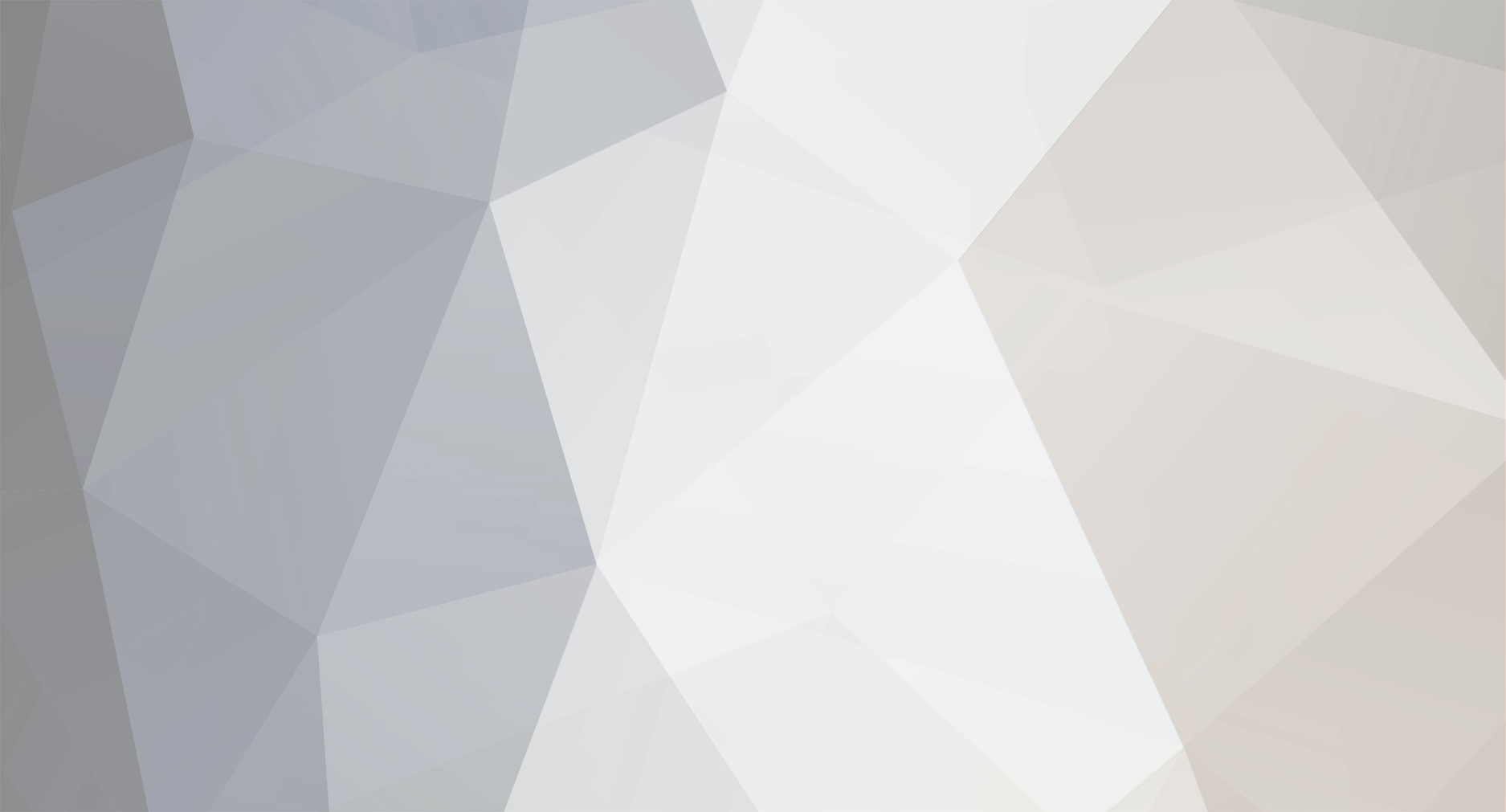
BMW56
Members-
Content Count
91 -
Joined
-
Last visited
-
Days Won
1
BMW56 last won the day on April 25 2017
BMW56 had the most liked content!
Community Reputation
13 NeutralAbout BMW56
-
Rank
Advanced Member
Recent Profile Visitors
1,204 profile views
-
Quick follow up and thanks again for the advice. With some better weather I finally managed to get onto this. My initial plan to remove the backing plate turned out to be the wrong approach, however with the help of a couple of pry bars I was able to remove the thrust bearing from the plate. New parts installed and gearbox refitted today. The shaft was attached with a tension pin, which was all but completely corroded. Timely repair.
-
Thanks SloopJohnB. Hoping to have another look at this tomorrow. My plan is to start with the backing plate. I'm hoping then the whole shaft will move forward. Just got to deal to a heap of sealant that the builder or last person in there has used.
-
Thanks Ex Machina. Good advice there. I don't have access to the aft side of the bulkhead but the bearing is attached to a metal plate which looks to be removable. I presume that by removing the plate I'll be heading in the right direction and will be able to draw the whole assembly foward. Good suggestion to fit a new bearing while I'm at it thanks.
-
BMW56 started following Pulling prop shaft
-
Trying to remove the prop shaft to replace the cutlas bearing. Engine is out for overhaul. Attached is a photo of the thrust bearing/seal. Is anyone familiar with this sort and what is the best way to pull the shaft? There doesn't appear to be any obvious way to uncouple the shaft but maybe I need to remove the bearing first? Any pointers?
-
I built a new exhaust manifold and mixer from stainless 2 years ago. I made a template from PVC water pipe first then fabricated from off the shelf bends. Worked out well and no issues so far. Bends and tube from Steel & Tube Stainless. Price was reasonable and their rep was very helpful. Had a mate help with welding. Only downside was the time it took but I had no other option as the old manifold was badly corroded and no original replacement available.
-
Hi all, Not sure if anyone else on here has their boat moored at Cass Bay or Corsair Bay in Lyttelton Harbour. Unfortunately there have been multiple breakins to boats in the last couple of days, so it would pay to check your vessel. Also be on the lookout for any cheap boating gear offered for sale as is could be stolen property. I'm missing a Raymarine tiller pilot and a 5KW inverter as well as a few other bits. Cheers, Barrie
-
Definitely a good price. I paid more than that just for the materials for mine, though it had a couple more bends.
-
Combined effort. I had a mate help with the welding and he CNC machined the manifold flanges.
-
I promised I would share some photos so here they are. New exhaust manifold fabricated from Schedule 40 pipe and the exhaust pipe and mixing elbow. Fitted it all up and tried it out on Saturday and it works perfectly.
-
Talking about sanding antifoul, I have found using a tungsten blade paint scraper really handy for tidying up after water blasting. I have previously sanded (using No 5), but one of the guys in the haulout yard suggested I try this, and it worked a charm. Just takes a light run over to shift any lumps and bumps. I should say I'm not looking for a mirror finish but it was a huge time saver.
-
Thanks again for the replies. Fish, the contact for The Engine Room sounds worth a follow up and Frank, that was a useful link you provided. All good info. I'm breaking the job into two parts. The first is to fabricate a new manifold for the engine, replicating the original one as closely as possible, but in stainless. While we are doing that I'll investigate the options for the riser and mixing elbow. There's a bit of a plan taking shape, so I hopefully I'll be able to share some photos before too long (and be back on the water).
-
Thanks for the replies. I have somebody lined up to help with the fabrication. He's a first class welder and machinist, though not much marine experience. We have a plan for making a new manifold and intend to keep that separate to the riser and mixer to make future repairs easier. I'm still not happy with the idea of hot salt water sitting in the bottom of the riser and condensing into the exhaust manifold as the engine cools, so I'm keen to see if there's a better way to do it. The previous owner had exhaust valve problems and had to do a head overhaul, so I suspect the current set
-
Sadly the exhaust manifold and mixer on my engine has reached the end of its life and has failed fairly dramatically. The engine is an older Isuzu and the original cast iron manifold has corroded fairly dramatically to the point where it broke (fell) in half while dismantling. You will see in the attached photo there is a stainless water jacketed riser and mixing elbow which are custom made. The water jacket is really just a second point of injection into a well which the exhaust gases flow through, rather than a proper jacket. Parts for the Isuzu are hard to come by, so it looks as if w
-
This may be useful: Morse_MV-2_Owner_Manual.pdf (correctcraftfan.com)
-
I have the same unit and while it's working OK the aluminium plate has become quite corroded. I had a go at removing the whole unit but gave up after removing the screws on the face plate and finding it was still well attached. It was going to be more complicated than I had time for that day so it's gone to the to-do list, but some maintenance is probably well overdue. To save me some mucking around, is somebody able to advise the best way to detach and remove the unit please? I'm thinking it may be fastened from behind where I can't see. Thanks.